Briefing
MAN Energy Solutions
MAN Energy Solutions Switzerland AG is one of the leading manufacturers for centrifugal gas compressors. In order to compress the gas, it is being accelerated by radial wheels and redirected into a diffusor – pressure is being increased. You can find a detailed description of centrifugal gas compressors here.
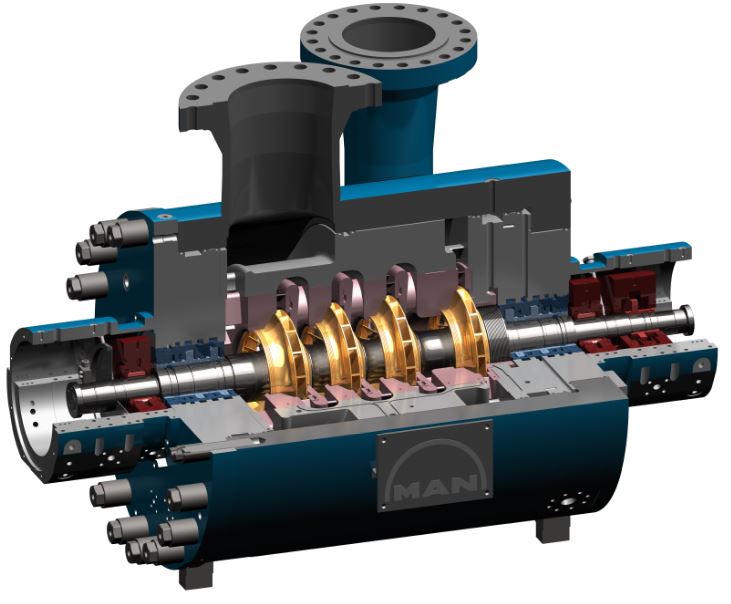
Task
New application processes and new materials are wanted to substitute or improve the current complex and costly technology with the aim to guarentee a longterm life of uninterrupted operation of our machines.
Status Quo
Currently, the compressor manufacturers are using in case of a severe corrosive environment the following material options:
- Inconel 625 / 2.4856 or Inclonel 718 / 2.4668
- Inconel 625 Cladding applied to carbon steel by welding process
- Duplex steel 22Cr Duplex / 1.4462
However, these materials and the application of a welding layer are very time consuming and therefore costly.
Background Information
The surface protection to be developped shall meet the following requirements:
- Temperatures, pressure etc.
- Corrosion resistant, values CO2 / H2S / Partial pressures / Ph
- Chlorides 100 ppm
- Hg / Mercury 20 ug / Nm3
- Errosion resistant, values 0.001 mm / year
- Durable for up to 25 years service life
- Good connection to the base layer (no peeling off)
- Applicable for components up to 1500mm in diameter (static)
- Applicable for complex shapes such as i.e. impellers (dynamic)
- Quality assurance with existing test methods
- Proven industrial application / technology
C02 75 content mol%
H2S 16.4 content mol%
6-10 % H2O
C02 partial pressure 3.77 barg
H2S partial pressure 0.82 barg
Ph 3.5
Further information: Material Properties
Explanation
- Industrial turbocompressors with a power intake of >1MW are used in a broad field of applications. The application field ranges from upstream, midstream to downstream in the oil & gas sector and also includes the application of industrial gases.
- In all of these applications the turbocompressors are designed to compress gas with a suction pressure ranging from 1 to 400 bara and a discharge pressure ranging from 2 to 800 bara at a maximum stage discharge temperature of 220°C.
- The conventional turbocompressor consists of oil bearings attached to the casing covers, a pressure containing casing, casing covers with the shaft seals sealing the compressor internals from the atmosphere, a rotating shaft with up to 10 impellers and stationary internal parts exposed to the process gas.
- Turbocompressors are known for its reliability and for its very long Mean Time between Overhauls and thus the longevity of the material is amongst others an important factor for the design of such turbocompressors.
- Especially in the application field “upstream” the requirements to the material choice is usually very demanding when it comes to the corrosion aspect. As such, the following corrosion mechanisms are mostly affecting components exposed to the process gas: General corrosion, Pitting Corrosion, Stress Corrosion Cracking and Sulfide Stress Corrosion Cracking. Rotating parts are usually exposed to stress induced corrosion whereas the stationary parts are more exposed to general corrosion and pitting corrosion.
- The corrosion rate is mostly dependent on the Ph content of the process gas, the CO2 and H2S content and the presence of an electrolyte which can also be condensate water.